Applicable à Cat 330D / 336D Capteur de pression d'huile EX2CP54-12
Introduction du produit
Le capteur de pression a une précision élevée et une erreur raisonnable, et la compensation d'erreur du capteur de pression est la clé de son application. Le capteur de pression inclut principalement l'erreur de décalage, l'erreur de sensibilité, l'erreur de linéarité et l'erreur d'hystérésis. Cet article introduira le mécanisme de ces quatre erreurs et leur influence sur les résultats des tests, et introduira en même temps la méthode d'étalonnage de pression et les exemples d'application pour améliorer la précision de mesure.
À l'heure actuelle, il existe de nombreux types de capteurs sur le marché, ce qui permet aux ingénieurs de conception de choisir les capteurs de pression nécessaires par le système. Ces capteurs incluent non seulement les convertisseurs les plus élémentaires, mais aussi des capteurs à haute intégration plus complexes avec des circuits sur puce. En raison de ces différences, l'ingénieur de conception doit compenser autant que possible l'erreur de mesure du capteur de pression, ce qui est une étape importante pour garantir que le capteur répond aux exigences de conception et d'application. Dans certains cas, la compensation peut également améliorer les performances globales du capteur dans l'application.
Le décalage, l'étalonnage de la plage et la compensation de température peuvent tous être réalisés par un réseau de résistance à couches minces, qui est corrigé par le laser dans le processus d'emballage.
Le capteur est généralement utilisé en combinaison avec un microcontrôleur, et le logiciel intégré du microcontrôleur lui-même établit le modèle mathématique du capteur. Une fois que le microcontrôleur a lu la tension de sortie, le modèle peut convertir la tension en valeur de mesure de pression par la conversion du convertisseur analogique-numérique.
Le modèle mathématique le plus simple du capteur est la fonction de transfert. Le modèle peut être optimisé dans l'ensemble du processus d'étalonnage, et la maturité du modèle augmentera avec l'augmentation des points d'étalonnage.
Du point de vue de la métrologie, l'erreur de mesure a une définition très stricte: elle représente la différence entre la pression mesurée et la pression réelle. Cependant, la pression réelle ne peut pas être obtenue directement, mais elle peut être estimée en adoptant des normes de pression appropriées. Les métrologues utilisent généralement des instruments dont la précision est au moins 10 fois plus élevée que celle de l'équipement mesuré comme normes de mesure.
Parce que le système non calibré ne peut utiliser que des valeurs de sensibilité et de décalage typiques pour convertir la tension de sortie en erreur de pression.
Image du produit
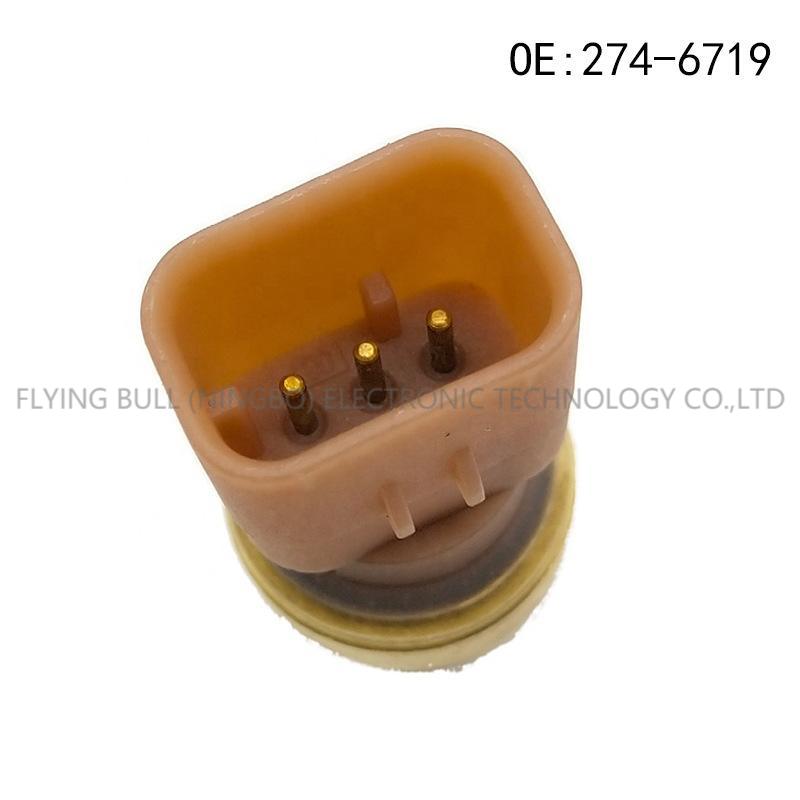
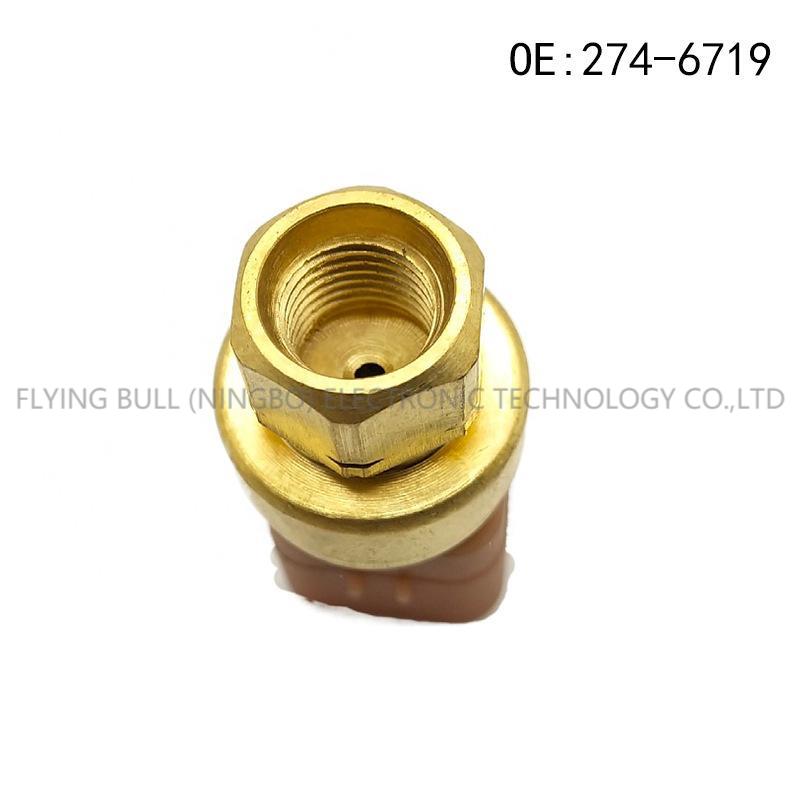
Détails de l'entreprise

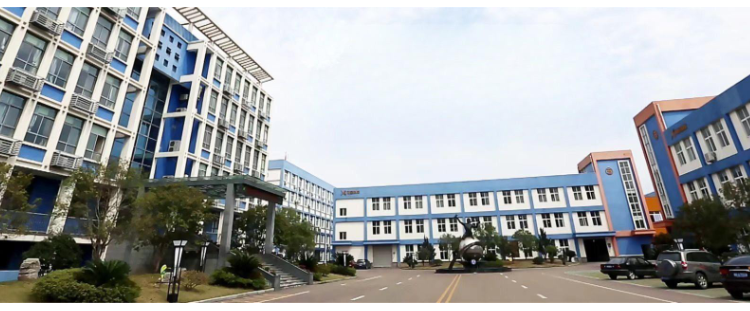
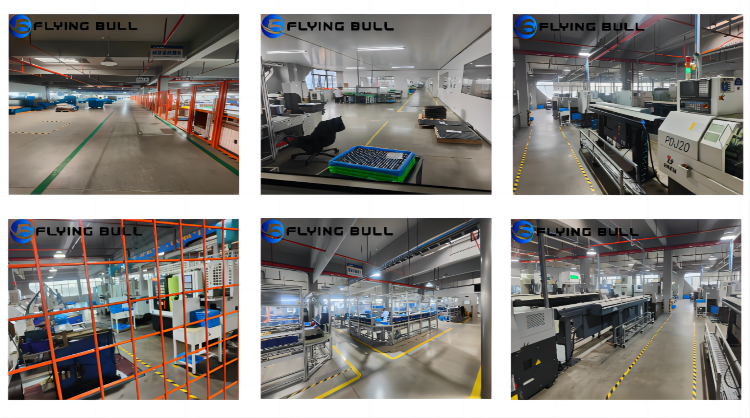
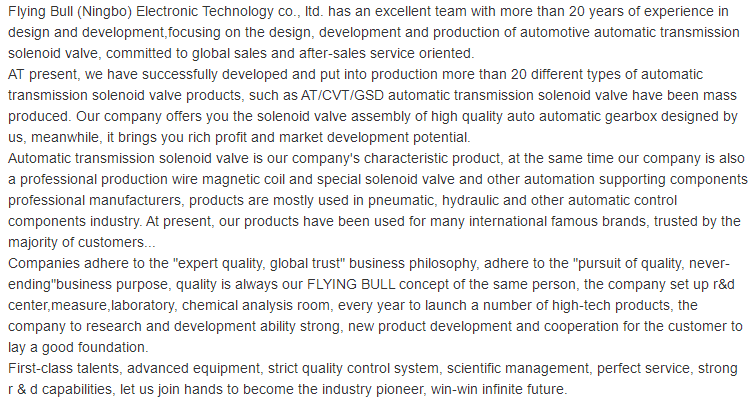
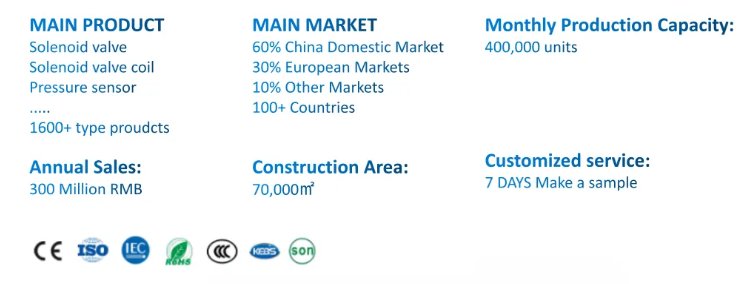
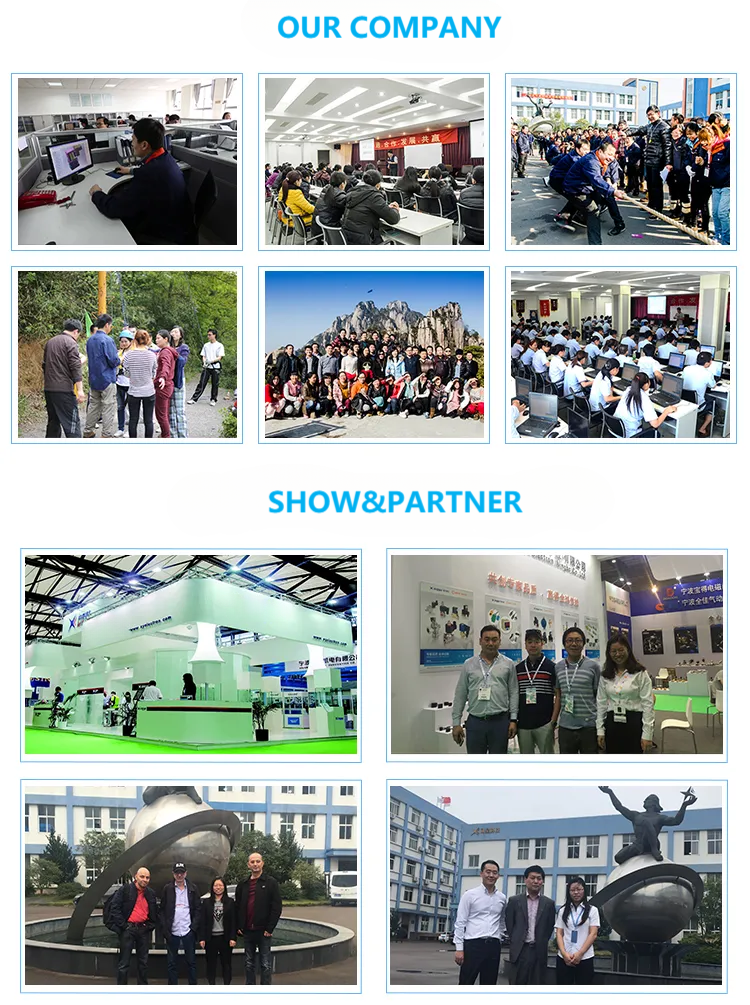
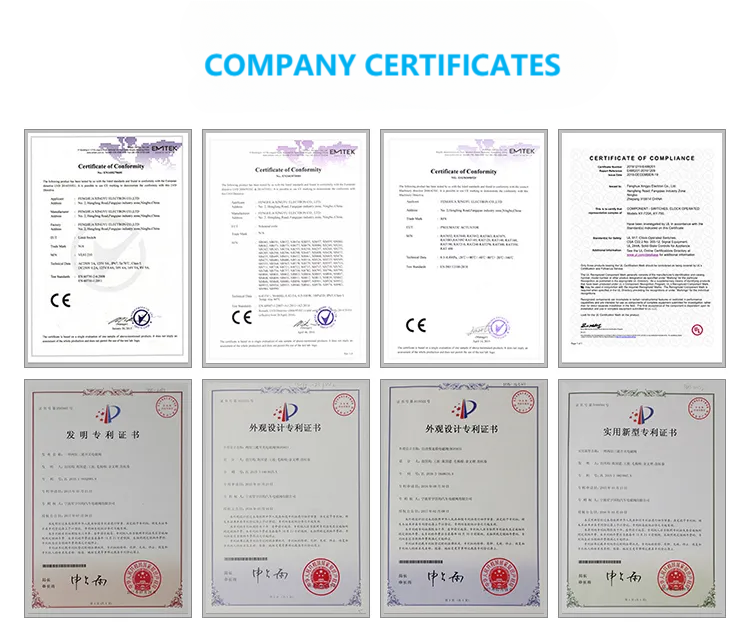
Avantage de l'entreprise
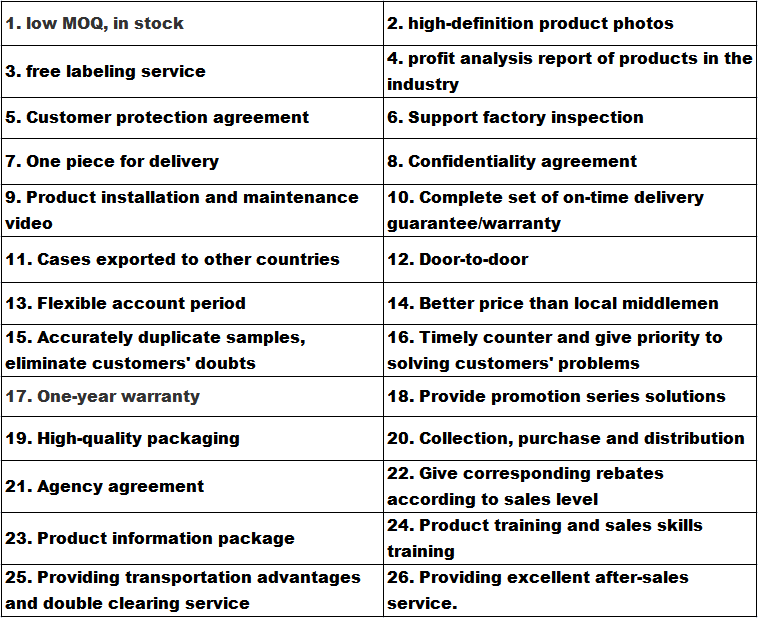
Transport
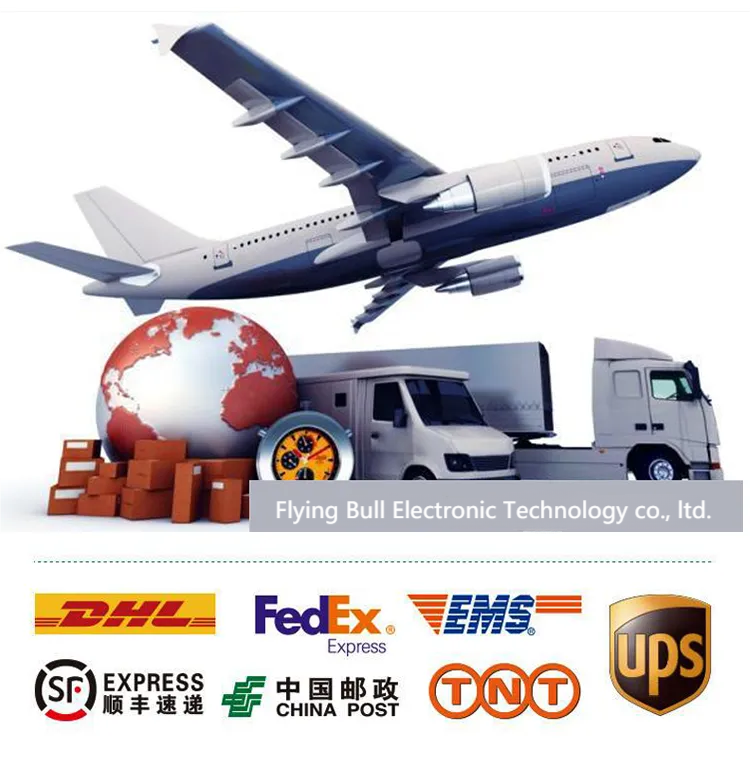
FAQ
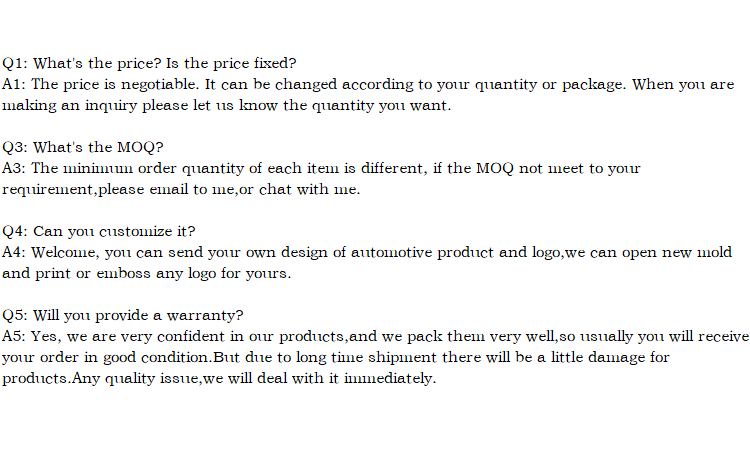